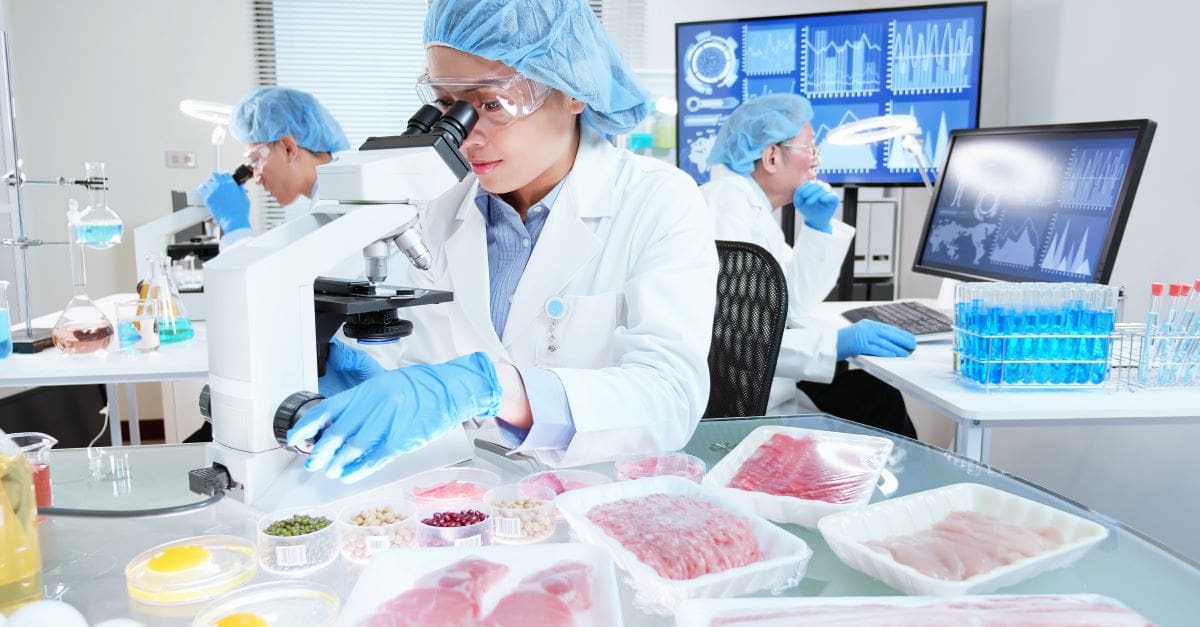
Lasagna noodles are characterized by a long, rectangular shape with rippled edges. If those edges aren’t rippled properly (e.g., spacing, height, etc.) the correct weight of the product won’t fit into the box designed for it and the customer won’t get the amount of product they paid for. That’s just one small detail of product packaging, which makes up one of the three major segments of the food and beverage industry, along with food processing and distribution. The food we purchase, the restaurants we may visit, and the products we distribute are all part of a complex industry.
Key issues for the food and beverage industry
The food and beverage industry is under continuous pressure to improve products, reduce costs, provide better services, and, particularly in 2022, get products produced and delivered to where they are needed. While those are the most visible to the consumer, for the industry itself there are eight issues1 that are their primary focus: plastic elimination, health awareness, inventory management, veganism, regulations, product traceability, COVID-19 impact, and e-commerce penetration.
Plastic elimination
Plastic materials have found widespread use in food product packaging; everything from coffee cups to prepared meals in containers that let you see the product while keeping it free from contamination. While convenient, plastic items are under increasing criticism, from complaints of filling landfills with slowly decomposing products, to recent health concerns about microplastics affecting the environment and our health. The industry is under pressure to eliminate plastic wherever it can, replacing it with more biodegradable options.
Recycling is also part of the process as it reduces the need for introducing new plastic into the system by reusing existing materials. However, some plastic-containing materials aren’t readily recyclable. For example, many recycling centers can’t recycle bottle caps because of the mix of materials used; the cap is often a different polymer than the bottle. These and other pressures have resulted in companies like Heinz closely examining their packaging. In fact, Heinz spent 185,000 hours redesigning its ketchup bottle cap to improve its ability to be recycled2.
Health awareness
People are increasingly aware of the benefits of some foods and the detrimental effects of additives. As a result, consumers are becoming more health conscious, gaining a preference for products that support a healthy diet and looking for labels with “dairy-free,” “gluten-free”, and “sugar-free” to guide their purchases. In addition, food allergies are causing consumers to become more careful about the ingredients in products, taking producers to task if miss-labeling occurs. In turn, those producers must then be agile with food recalls avoiding litigation, protecting brand identities, and maintaining reputations.
Inventory management
Food products have a limited shelf life, leaving distributors to walk the fine line between leaving products on the shelf too long and running out of a desirable product too quickly. In other words, inventory management is a balance between satisfying customer demand for products and having them become waste because they have passed their “sell-by” date.
Veganism
Consumers are becoming increasingly concerned with the treatment of animals used in food production. In fact, animal abuse awareness has grown to the point where people are looking for labels with “humane-certified” and “cage-free” on them. Others are avoiding the issue by eliminating meat from their diets and looking for plant-based products that either look and taste like meat, or (eventually) meat products that are lab-grown. Note: lab-grown meat isn’t technically vegan since it must not contain animal products or by-products3.
Regulations
The industry is governed by the Food and Drug Administration (FDA), the Environmental Protection Agency (EPA), Occupational Safety and Health Administration (OSHA), and the Federal Trade Commission (FTC). The US Department of Agriculture (USDA) also plays a role in ensuring the health and safety of food products through the USDA’s Food Safety and Inspection Services (FSIS)4.
Product traceability
The traceability of finished products, ingredients, and other additives is becoming increasingly important as consumers want to have trust in the safety of the products they are consuming. It’s a key factor in product quality control and ensuring that products are safe to use.
Impact of COVID-19
COVID-19 had a major impact on the food and beverage industry. Concerns about people working in close quarters during food production and preparation played a significant role in the industry’s downturn in recent years. Production and distribution facilities – including restaurants – had to modify the design of their workplaces to minimize the opportunity for disease transmission. This is going to play a continued role in managing facilities as COVID continues to be a problem along with other pathogens.
E-commerce penetration
In comparison to electronics manufacturers, the food and beverage industry has been slower to take advantage of the Internet and its potential. However, the industry is gradually adopting more modern paradigms like web-based services for food delivery and shopping as technology-savvy companies start using electronic systems to assist shoppers in cataloging their purchases and making checkout easier. Some restaurants are using web-based apps for ordering take-out items and making payments. This may push smaller operations to adopt these technologies for greater customer convenience.
Research
To meet these demands, the food and beverage industry is conducting a great deal of research towards developing new, more appealing products and packaging and product transportation concerns. The 1970s saw a concerted effort to replace glass in beverage containers, particularly carbonated beverages like soda. When a bottle was dropped and broke, it not only spread the liquid around but also propelled broken glass outward, sometimes causing injury to people. A number of approaches were tried including covering the glass with plastic to contain the glass if it was dropped and broken. The plastic soda bottles we have today, made of polyethylene terephthalate (PET), are the result, offering a lightweight alternative resistant to breakage and leaking carbon dioxide, which would let the soda go flat. This led to other plastics being used in other food packaging.
The research facility can consist of a wide variety of venues, including a computer-aided design system for modeling packaging, a plastics fabrication facility, and a test kitchen, as well as a typical laboratory bench. The testing process can also vary widely to include standard chemical tests, and physical property tests to evaluate packaging and food consistency (e.g., changes in food viscosity as it ages). Testing may also include sensory-based testing such as the taste, appearance, and smell of both the food and the packaging, as some plastic material additives can degrade over time and cause offensive odors.
Also vital to the food and beverage research process is lab-based accelerated aging tests, which can aid in predicting the shelf-life of products, and are the origin of those “best used by” dates on food containers. This is a sophisticated process that can generate a lot of testing and cost. Products are subjected to both normal environmental and increased temperature parameters, and they are also exposed to light to mimic accelerated aging. However, care must be taken during testing such that increased temperatures don’t cause unwanted side effects like separations of materials.
In order to reduce the cost of accelerated aging tests, the aging process is applied to two sets of the same product whose accelerated aging may start a couple of weeks apart. The one that is started first is checked periodically to see if any product breakdown becomes evident. When that occurs, the second set is checked more frequently to pinpoint the time at which the breakdown occurs. This allows for the development of accurate aging data while minimizing the cost and effort involved. (We’ll come back to this when we discuss service labs and laboratory information management systems [LIMS].)
Research and product development projects will vary widely in complexity. A new food or beverage product can consist of the material or liquid itself, packaging, labeling, and test panels to evaluate the proposed product. However, regardless of the nature of the research, there are elements that are common to most research projects, including:
- Project description, including the entire program or a subset of the activities (e.g., new food product may have the overall project elements noted in the previous paragraph, or be one component, like the food recipe leaving the remaining items for other projects);
- Planning;
- Development and experimentation;
- Data and observation analysis;
- Communicating and sharing results; and
- Preparing documentation, reports, patent filings,
Some research work, particularly lab-based activities including test kitchens, could benefit from laboratory informatics systems. There are four tiers of laboratory informatics that can be used in that process. The informatics systems among those tiers (Table 1) include electronic laboratory notebooks (ELNs), laboratory information management systems (LIMS), scientific data management systems (SDMS), laboratory execution systems (LES), and instrument data systems (IDS).
Tier | Technology | Usage |
1 | ELN and LIMS | These are top-tier systems used to organize data/information. They can serve as information aggregators, organizing experimental results and observations. In research work, LIMS systems are subordinate to ELNs and are used to manage routine test workflows with the results of a series of tests summarized in the ELN. |
2 | SDMS and LES | SDMS and LES are support systems for ELNs and LIMS. An SDMS will organize and store data, files, and documents that don’t fit in the structure of a LIMS or ELN. A LES provides a means of rigorously executing a laboratory procedure with all data and information about that procedure being sent to the LIMS or ELN. LES’s are primarily used in regulated environments (e.g., FDA and EPA) or where strict adherence to a procedure has to be documented. |
3 | IDS | Instrument data systems (IDS) are a combination of instruments and computer systems. Common examples are chromatographic data systems (CDS) connected to one or more chromatographs. In addition, mass spectrometers, and almost any other major instrument category have similar capabilities. |
4 | Measurement devices (e.g. pH meter, balance) | At the lowest tier are devices like pH meters, balances, and other devices that have no internal permanent data storage associated with them and have to be programmed to be used with upper-tier systems. They can have their measurements transferred electronically under program control. They can also be used in a manual mode with data entered manually into a LIMS, ELN or LES, but in regulated labs, the input has to be verified by a second individual. |
Table 1: A tiered structure for laboratory informatics and measurement device technologies.
The most likely tools used in research are those in Tier 1; ELNs are used to record the details of projects and their development, and LIMS are used to record the results of testing which may be part of the research lab or sent to a third-party service lab for test work. (Service labs can also provide a quality control function where needed.)
Service lab operations
Product testing is an essential part of product development and research, as well as production in the form of quality control. That testing can be extensive, as can be the record-keeping and management of testing programs. Fortunately, such work can be done more easily with the aid of a LIMS.
LIMS has three functions that help support laboratory testing:
- Workflow management – What work is coming in? What has to be done? What are the priorities? What results have to be approved and released? These are routine questions that occur in any production operation and testing labs are a prime example. These and related questions to lab operations are addressed by a LIMS. As part of its operations management samples can be logged in at the lab or remotely (and then identified as “in the lab” when they arrive). This makes it easier to keep track of work that is coming in and plan each day’s testing
- Results management and data logging/capture – LIMS provides a complete database for capturing and organizing samples and test Results can be entered manually, or for more efficiency via electronic data/information transfer from instruments and IDSs. Most major IDSs have programming interfaces that permit downloading of work that has to be done through the IDS, and then upon completion permit sending the sample ID’s and results back to the LIMS. This avoids manual data entry, greatly improves productivity, and provides a basis for 24/7 operations.
- Regulatory support – This is an important aspect of a LIMS It provides traceability for data; if results are challenged, the lab can respond to it by looking at the data history (including audit trails), who carried out the analysis, and who approved the results. The lab can also see what equipment was used and verify its readiness for use. This becomes important when labs have multiple responsibilities, for example to the FDA and the EPA.
One important type of testing described earlier is product stability or shelf life testing. Many LIMS have templates for this type of work. The analyst describes the time period for testing, how frequently testing is done, and the tests to be performed. The LIMS then creates the testing schedule and database entries to receive the results.
The actual details of service laboratory testing will depend on the nature of the products. The following list provides some examples of such testing.
- Nutritional testing: This testing is performed to ensure that components are present in the amounts noted on the labels and that potentially harmful items are not present.
- Microbiological testing: About 48 million people in the U.S. (1 in 6) get sick, 128,000 are hospitalized, and 3,000 die each year from foodborne diseases, according to recent data from the Centers for Disease Control and This is a significant public health burden that is largely preventable. The Food Safety Modernization Act of 2011 (FSMA), required many manufacturers to establish “preventative control” systems – closely modeled after hazard analysis critical control points (HACCP) and increase regular food microbiological testing for quality assurance purposes5.
- Pesticide residue screening: This testing ensures limits for pesticide residues are not
- Heavy metals testing: This testing ensures limits for toxic heavy metals like cadmium and lead are not exceeded.
- Allergen testing: This testing ensures that food labeling directives and regulations concerning allergens are effectively met.
- FDA import detention testing: When products in your shipment violate or appear to violate FDA laws and regulations, the FDA may detain your product and issue a Notice of FDA Action with the designation of “Detained.” Some laboratories provide testing services that are used to evaluate the FDA’s claims and if appropriate seek relief from their charges6:
- Bottle cap tightness – Ever have trouble opening a bottle because the cap is too tight? Manufacturers can set parameters on how much torque it takes to open a bottle, both minimum (to prevent leaks), and maximum (so that the bottle can be opened easily). Automated equipment is available to carry out this testing process.
In closing…
The food and beverage industry is under pressure from a variety of fronts, including a need to meet customer demand for nutritious, safe products; address environmental concerns like waste management and reduction; keep products on shelves, and meet the demands of multiple regulatory agencies are just a few points, all while making a profit. Laboratory informatics can play a significant role in increasing the efficiency and productivity of that research and testing. LabLynx’s ELab LIMS software solution, in particular, can support everything from materials evaluation in research to quality control during and after products are produced. Among their benefits are clear, searchable documentation about products and their production, tracebacks in the event production quality is challenged, and improved communications throughout the cycle, from research, testing, and product evaluation to production, packaging and distribution cycle.
The ability to choose between on-premise or cloud-based LIMS implementation means laboratories can optimize their system characteristics to have consistently reliable data structures, reduced cost of maintenance and support, and improved communications throughout their product development and quality management programs cycles.
Footnotes
1 https://www.gminsights.com/blogs/challenges-in-food-and-beverage-industry
2 https://www.fastcompany.com/90805336/why-heinz-spent-185000-hours-redesigning-this-ketchup- bottle-cap
3 https://www.livescience.com/lab-grown-meat and https://scienceline.org/2019/01/the-truth-about-lab-grown- meat/
4 https://www.usda.gov/topics/health-and-safety
5 https://www.fda.gov/food/guidance-regulation-food-and-dietary-supplements/food-safety-modernization-act-fsma
6 https://www.fda.gov/industry/fda-import-process/detention-hearing#lab