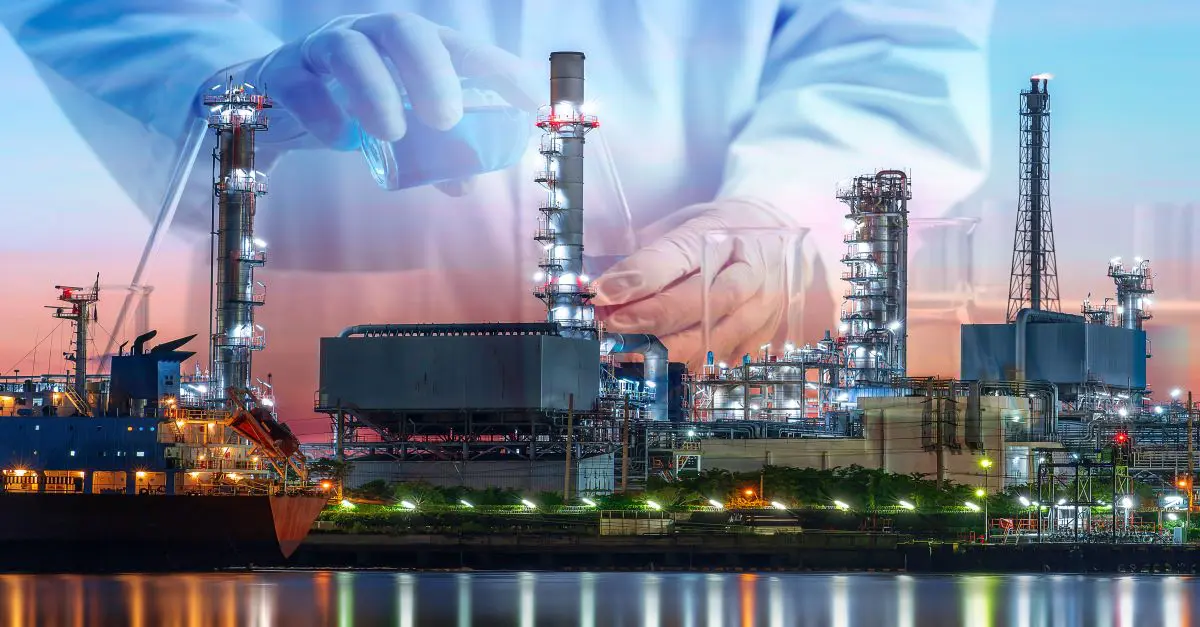
When I was younger, we had black and white TV (three channels!) and were told that oil came from dinosaurs; it said so in the TV commercials. Now we have color displays and different ideas about where oil comes from (or how much is left). There are different theories about oil’s origins. The prevailing theory has oil coming from decaying organic matter at the bottom of ancient seas.1 Some of that matter could be aquatic animals and maybe a few dinosaurs, but most of it is plankton. Today we have a lot more information about what happens to that oil.
Introduction
In the next few sections, we’re going to look briefly at the petrochemical industry and the production efforts that are derived from it and then look at the roles that informatics systems play in research and service lab support operations, including testing support, quality control, and the informatics-supported instrumentation of inline process control.
The oil that is pumped out of the ground is the essential starting point for the industry’s manufacturing and production operations. In 2021, the US consumed 19.78 million barrels per day including about a million barrels of biofuels.2 The major end-use sectors consist of transportation (67.2 percent of that production), industrial (26.9 percent), residential (2.8 percent), commercial (2.5 percent), and electric power (0.5 percent). That production found its way into:
- Fuels for internal combustion engines, jet engines, heating systems, etc.;
- Feedstock for chemical products including plastics, medicines, coatings, etc.;
- Parts for vehicles including tires, car seats, bumpers, the plastics used in the interior/exterior as well as fuels and lubricants;
- Construction materials such as roofing, sealants, plastics (including coating for trim and window components), tools, wiring insulation, plumbing, etc.;
- Accessories such as smartphones, jewelry, and eyeglass frames;
- Textiles that are used in clothing and other applications;
- Household and medical applications such as appliances, hospital beds, combs, toothbrushes, and cosmetics;
- Electronics containing large amounts of plastic in their equipment housing and components (particularly in printers); and
- Toys, office accessories, agricultural applications, and more.
In short, the petrochemical industry affects almost every aspect of our lives and civilization to the point where a major concern is what to do with these materials once they’ve satisfied their initial usage. Recycling used products is a growing problem that is being attacked on a number of fronts. What I’d like to highlight here is the work done on recycling used oil. This is important in this discussion because it opens another avenue for lab operations to participate in this industry.
Used oil isn’t “bad oil” or “used-up oil”, but rather dirty oil that can be recycled and repurposed if it is cleaned up.3 During its use, lubricating oils (e.g., engine oil) can pick up dirt and metal shaving that over time can cause deterioration of the structure of the oil, but if removed, can create new products such as biodiesel fuels, lubricants, and feedstock into chemical production. Both research and service laboratories are needed to develop these new products, develop new methods of recycling oils, and analyze the resulting materials for the characteristics needed in those next stages of production.
Throughout this set of industries, we find oil and gas laboratory applications distributed across three phases: the initial product and feedstock production, the conversion of the feedstock to products, and the recycling of used products to new sources of raw materials. The efficient and thorough utilization of these materials is important not only for the health of the basic industries that depend on them, but also because the supply/demand relationships become significant geopolitical factors in worldwide economics and policy decisions concerning international relationships and climate change.
The processes used in facilities to convert feedstock materials to products are examples of continuous production methods. They run 24 hours a day, seven days a week, and they rarely shut down. In most cases changes in product characteristics (e.g., a different product being produced), are accomplished by a gradual change over in production conditions and materials with the intermediate materials sold as scrap. This avoids a potentially costly production shutdown, which later requires that the production system be cleaned, inspected, and then restarted. The costs of a shutdown can be measured in lost production time, and the resources required for cleaning. Restarting a process can also take time since the production system has to come up to a stable operating condition before it is producing a product that meets the specifications for that material.
Laboratory operations
Throughout the production process, one type of service laboratory will play a significant and potentially changing role in making sure that the operations are running smoothly and that any abnormalities are flagged: the quality control (QC) lab. The details of a service lab’s operations will be covered below. In addition to QC, service labs provide support by performing analytical chemistry analysis, physical properties measurements, and materials characterization evaluations. These support both production and research operations. Before we examine their roles, we’ll look at QC’s four main functions in oil and gas production operations (Figure 1).
As Figure 1 denotes, the production process samples would be taken at set points during the process and prior to production output. These points, designed in the system during its planning, are there to provide a measurement of the process’s health so that potential issues can be detected and corrected early and avoid the creation of scrap materials. Depending on the nature of the process, these sampling points can be of two types: places where physical samples can be taken, and at the instrumentation to measure key aspects of the process. Physical samples are taken back to the QC lab for evaluation. In-line instrumentation can either take continuous samples (e.g., spectrophotometric) or periodic samples such as those taken by automated process chromatographs.
Before the advent of instrument data systems (IDS) to collect and analyze instrument output, in-line instrumentation was the responsibility of the QC lab, whose tasks included making calibration checks, developing a calibration chart for the device, and performing the measurements and calculations needed for each instrument. Now that we have computers to automatically carry out the analysis needed for each instrument, the QC task list might be reduced to instrument maintenance and calibration checks with the computer taking on the routine data analysis and sending the results directly to process control.
Automation is changing the role of the QC lab and the specialists within it. Some tasks —particularly physical properties measurements, and the evaluation of the finished product — may always remain a human effort due to the difficulty in automating them. However, automation is going to reduce the workload of the quality control lab; an organization whose role may evolve over time.
In addition to QC labs, the oil, gas, and chemicals industries utilize the capabilities of research labs and other service lab organizations. Those service labs include:
- Analytical chemistry groups that perform testing in support of research and test method development (some of which are used in QC labs) and conduct both routine and non-routine testing and analysis.
- Physical properties groups which are similar to analytical chemistry groups but focus on the physical properties of materials (e.g., color, viscosity, density, etc.), depending upon the process and products.
- The materials characterization group, which follows the same activities noted in the other groups, but with an emphasis on examining the rheological characteristics of fluids, molecular weight distribution, thermal analysis (e.g., differential scanning calorimetry, thermogravimetric analysis), etc.
While some of these laboratories may develop their own test procedures, many others rely on organizations such as the ASTM International4, the American Petroleum Institute (API) and other trade associations for standardized procedures. They also conduct testing to meet environmental regulations provided by the Environmental Protection Agency (EPA).
Research groups are often tasked with developing new products, improving existing products, or improving/optimizing the production process to achieve better economics, meet environmental regulations, or improve product characteristics.
Laboratory accreditation
The laboratories in these industries need to be accredited to the ISO 170255 standard (designed to demonstrate technical competence for analytical results as well as the lab’s management structure) and any relevant industry regulations that cover their production operations. Most are governed by the International Organization for Standardization’s ISO 9000 family of regulations, but they may also fall under the purview of the Environmental Protection Agency (EPA), Food and Drug Administration (FDA), and trade group requirements. The Bureau of Land Management (US Department of the Interior) may also impose accreditation requirements as part of its inspection and enforcement efforts for oil well sites on federal and Indian land.6 Finally, oil and gas labs may also seek certification by the American Association for Laboratory Accreditation (A2LA).7 The A2LA is the largest independent accreditation organization in the world and operates as a non-profit organization.
Informatics in laboratory work
Research
Research and product development projects in the oil and gas industry will vary widely in complexity. However, regardless of the nature of the research, there are elements that are common to most research projects, including:
- Project description, including the entire program or a subset of the activities;
- Planning;
- Development and experimentation;
- Data and observation analysis;
- Results communication and sharing; and
- Preparation of documentation, reports, patent filings, etc.
Some research work could benefit from laboratory informatics systems. These are data collection, and database systems that act as data aggregators/concentrators, taking data and information from instruments and observations, and then organizing them to be more easily used thus increasing their value to the organization.
The use of laboratory informatics in research can:
- Improve communications by giving more people easier access to the data they need to make decisions — making data sharing easier and more effective since it can be placed in a common format — while enabling security controls to prevent unauthorized people from accessing confidential information;
- Help coordinate the work of different research groups;
- Give better insight into the lab’s data and information;
- Improve the economics and efficiency of research programs;
- Provide better control with increased security over the lab’s data; and
- Allow for better decision-making about the direction of research programs.
There are four tiers of laboratory informatics that can be used in that process. The informatics systems among those tiers (Table 1) include electronic laboratory notebooks (ELNs), laboratory information management systems (LIMS), scientific data management systems (SDMS), laboratory execution systems (LES), and IDSs.
The most likely tools used in research are those in Tier 1; ELNs are used to record the details of projects and their development, and LIMS is used to record the results of testing which may be part of the research lab or sent to a third-party service lab for test work. (Service labs can also provide a quality control function where needed.) Large projects can benefit from cloud-based systems to share data between geographically dispersed facilities.
Service lab operations
Material testing is an essential part of product development and research, as well as production in the form of quality control. That testing can be extensive, as can be the record-keeping and management of testing programs. Fortunately, such work can be done more easily with the aid of a LIMS.
LIMS has three functions that help support oil and gas laboratory testing:
- Workflow management – What work is coming in? What has to be done? What are the priorities? What results have to be approved and released? These are routine questions that occur in any production operation and testing labs are a prime example. These and related questions to lab operations are addressed by a LIMS. As part of its operations management samples can be logged in at the lab or remotely (and then identified as “in the lab” when they arrive). This makes it easier to keep track of work that is coming in and plan each day’s testing schedules.
- Results management and data logging/capture – LIMS provides a complete database for capturing and organizing samples and test results. Results can be entered manually, or for more efficiency via electronic data/information transfer from instruments and IDSs. Most major IDSs have programming interfaces that permit downloading of work that has to be done through the IDS, and then upon completion permit sending the sample ID’s and results back to the LIMS. This avoids manual data entry, greatly improves productivity, and provides a basis for 24/7 operations.
- Regulatory support – This is an important aspect of a LIMS’ capabilities. It provides traceability for data; if results are challenged, the lab can respond to it by looking at the data history (including audit trails), who carried out the analysis, and who approved the results. The lab can also see what equipment was used and verify its readiness for use. This becomes important when labs have multiple responsibilities, for example to the EPA as well as corporate management.
While a LIMS provides facilities for data collection and organization, it also has functionality that can be used to improve communications between testing labs and those submitting work to the lab. This is particularly important in the QC lab, where communication between that lab and process control is critical. For example,
- Process control has to be kept updated on the status of testing and results so that it can make real-time decisions about the state of the production process and any anomalies that might occur. The LIMS may have a direct interface with process control and production management systems including enterprise resource planning (ERP), manufacturing execution systems (MES), product lifecycle management (PLM), and batch records systems.
- The receiving department needs to make QC aware that new raw materials have arrived and have to be evaluated. Once that is done, QC has to notify receiving and production that the material is certified as ready-to-use.
- The QC lab has to notify the shipping department that materials are either ready to ship to customers or, that some aren’t suitable for dispersal and have to either be reworked (if possible) or sold as scrap.
In closing …
Modern laboratory informatics systems are essential to the efficient operations of both oil and gas production facilities and related research work. In research, ELNs can manage the progress of research projects with LIMS providing support for extensive routine testing programs. In service lab operations the dominant system will be the LIMS; however, in groups that carry out test method development projects, an ELN may play a supporting role. An SDMS will provide support for research and service labs supporting research by providing a means of organizing large data files and documents. And IDSs support both research and service lab operations, streamlining the process of data generation, collection, analysis, storage, and reporting.
With all of this data and information being produced, it is incumbent upon the oil and gas labs and their IT support to provide reliable and regular systems backup and data management so that important current and historical data is not only securely retained, but is easily accessible/recoverable as needed. This data will be necessary to support regulatory compliance and legal challenges if products are found to be suspect in customer applications.
With a well-designed laboratory informatics architecture and attention paid to technology management and planning, a laboratory informatics system can provide a solid basis of support for a petrochemical organization’s research, production, regulatory, and customer support needs.
References
1 https://www.howden.com/en-us/articles/pcog/where-does-crude-oil-come-from and https://www.thoughtco.com/oil-comes-from-dinosaurs-fact-or-fiction-3980636
2 https://www.eia.gov/energyexplained/oil-and-petroleum-products/use-of-oil.php
3 https://www.epa.gov/recycle/managing-reusing-and-recycling-used-oil
4 https://www.astm.org
5 https://17025store.com/iso-17025-standards/what-is-iso-17025/
6 https://www.blm.gov/programs/energy-and-minerals/oil-and-gas/inspection-and-enforcement
7 https://a2la.org/about/