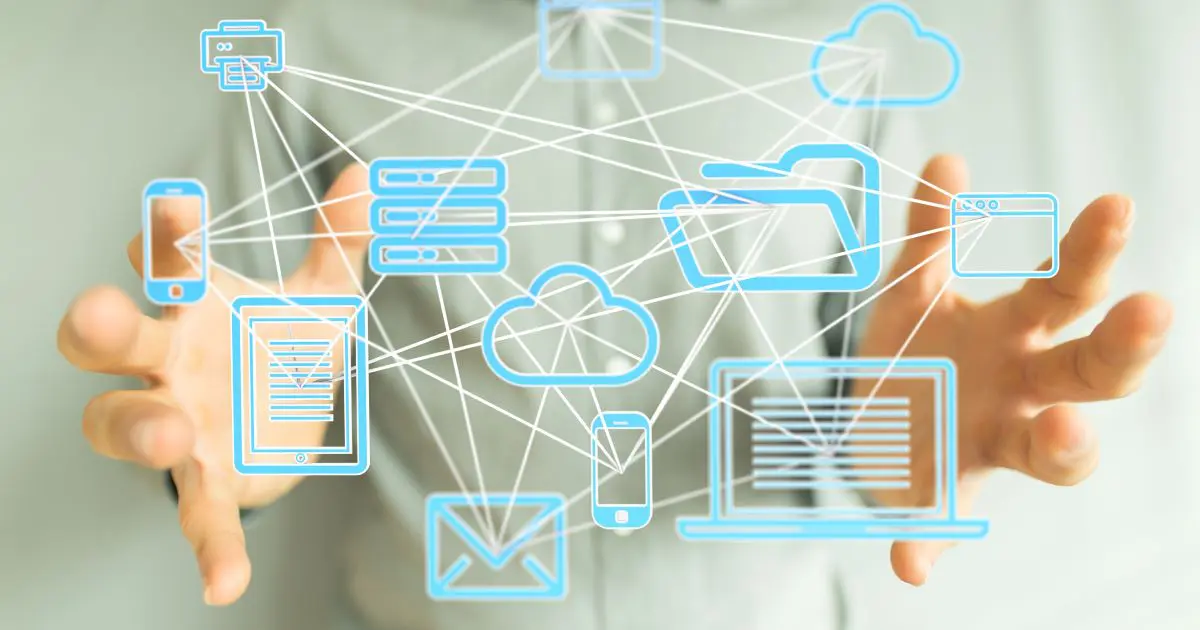
Laboratory information management systems (LIMS) are essential for managing data and information in modern laboratories. These software platforms help laboratories streamline their workflows, improve data accuracy, and enhance the efficiency of their operations. However, LIMS doesn’t work in isolation in today’s interconnected world. It needs to communicate with other systems, such as laboratory instruments, manufacturing and production systems, electronic health records (EHRs), and other software applications. This is where LIMS connectivity comes in.
This article will explore the importance of LIMS integration and connectivity and how it can benefit laboratories. We will discuss the connectivity options available, including application programming interfaces (APIs) and data exchange protocols. By the end of this article, you will better understand the role of LIMS connectivity in modern laboratories and how to implement it effectively.
Intra-laboratory connections
The opening paragraph mentions “improved data accuracy” as one of the benefits of having a LIMS in your laboratory. How do we accomplish that? In a related article entitled “Laboratory Informatics Systems Help Eliminate Data Entry Errors” we looked at the problems that can arise from manual data entry. Those errors include character transposition and transcription mistakes and the escalating costs that can occur if they aren’t caught early in the data entry process. One recommendation to help avoid these issues was to use electronic data transfer to automate data entry from laboratory instruments, avoiding manual methods where possible.
Laboratory instrumentation can be found in various forms, including analog, “smart” instruments, and instruments connected to computers, referred to as an instrument data system (IDS). Before we can talk about putting data into LIMS electronically, it must be digital. The general model for instrument automation is shown in Figure 1. The model is applicable to most lab instrument measurement processes and shows the major components of data collection systems and those needed for laboratory process automation. The goals are to first relieve the need for manual instrument readings, then convert data to a computer-compatible format and communications with higher-level software such as a LIMS or electronic laboratory notebook (ELN). The extent of the automation will depend on the sophistication of computer algorithms to control the instrument and the equipment needed to process and introduce samples for measurement and analysis.
In the beginning, there were analog measurements
Analog instruments (e.g., pH meters, mechanical balances, optical measurements, etc.) are the earliest instruments developed. However, it wasn’t until the 1960s and 70s that “digital smart/intelligent” commercial instruments became available, first with external computers and then with embedded microprocessors. From there the general transition to “digital” or “smart” devices began. While many labs have moved to smart systems, analog instruments are still widely used.
The issue that we need to deal with while using analog instruments and measuring devices is the conversion of a manual reading to a number that can be entered into a computer, like reading an alcohol or mercury thermometer. In this case, the analog-to-digital converter is you, taking a reading from the thermometer and writing it down. Because of the potential for errors in reading, writing numbers, and entering them into a computer we haven’t done anything to support the assertion of “improved data accuracy.” Resolving that problem is done by augmenting the device with a computer or microprocessor system to relieve manual data entry. In those cases, the reading of the analog signal is done using an electronic analog-to-digital converter (A/D or ADC) which provides a digital value that can be transferred to a computer’s processor for analysis, storage and communications. Doing so removes the manual readings from the workflow and provides error-free data transfer into the LIMS.[1] (Not all analog measurement devices are easily converter to electronic/automated readings without affecting or interfering in the measurement process. This is particularly true when measuring physical properties.)
Then things got “smarter”
“Smart” instruments are those with computer processors, storage, and communication capability placed within the instrument package such as digital pH meters, digital balances, etc.
An “intelligent” device – one with an embedded processor – has two modes of operation. The front-panel controls are used in manual mode and the rear-panel connections which can be connected to a computer. Those rear-panel connections can include ports for serial ASCII (e.g., RS-232, RS-485, etc.), USB, digital I/O, and Ethernet, as well as Bluetooth and Wi-Fi connections. In manual (front panel) mode, the analyst controls everything, and the results of the measurements are displayed on a numeric display. The alternative is to use programmed access to the device using the rear-panel or wireless connections.
Using rear-panel connections to a computer allows the analyst to have a program running through a LIMS or a standalone software application to control the device electronically. One example of this is an automated titrator controlled by a microprocessor[2]. The computer-instrument combination would require either a person managing the physical operations of placing samples and standards in the device or doing it under robotic control. In either case, the computer reads the measurements by sending a command to the device and receiving the response. It would then perform any necessary calculations and then prepare a table of samples, calculations, and results that can automatically be entered into a database such as LIMS. This eliminates manual data entry and provides a basis for automation and increased productivity.
Computers supporting one or more instruments
An IDS works similarly to a smart device, with computers taking on more of the work. At the analyst’s request, a LIMS would prepare a worklist of samples to be processed and send it to the IDS that controls the instrument and associated autosampler or other equipment. The autosampler would likely have a barcode reader to verify the sample being processed. The computer attached to the instrument would process the results, format a table of samples and results and send it to the LIMS for automated data entry. Again, this means no typing. The benefit is higher productivity, more efficient workflow, and lower cost of operations compared to manual method execution.
The major difference between many “smart” instruments and IDSs is not the list of hardware components, but the applications within which the instruments are used. For example, the process of using a chromatograph or mass spectrometer is consistent from one method to another across industries. As a result, the data acquisition, processing, and control functions are predictable and consistent with variations in hardware specifics; an autosampler might deal with vials in one application and gas sampling valves to introduce samples into the instrument in another. On the other hand, smart instruments such as pH meters, balances, and auto-titrators may be used in very different situations that aren’t predictable, and that limits the vendor’s ability to develop software for the end user. Instead, they leave the details of how the devices are used to those doing process automation.
Inter-organizational connections
Laboratories come in two organizational forms: as independent businesses serving a customer base and as part of a larger organization supporting research projects, manufacturing/production facilities, customers, and regulatory agencies. These communications include billing, sending, or receiving test results, and working with independent laboratories in addition to routine and non-routine reporting activities reporting. Most of these take the form of emails, or file transfers between database systems, in short, the routine computer traffic between systems.
Some may be time-critical such as patient health service through EHRs and quality control laboratories interactions with manufacturing execution systems (MES), product life cycle (PLM), document management (DMS), enterprise resource planning (ERP), and predictive manufacturing systems (PMS). In those cases, file transfers may not be sufficient, and more direct interactions between systems may be necessary.
Making the connections…
Our need for connections comes in two forms: real-time connections between instruments and computers, and, file transfers. Real-time connections are those that are time-critical, where systems or people need a response quickly to either continue with work (instrument connections during an experiment), or systems need to be notified of current conditions within a patient setting or production operation. Those may be routine data transfers or triggers for alarm conditions. File transfers using Transmission Control Protocol/Internet Protocol (TCP/IP) protocols between systems. These could consist of worklists, test results, charts of instrument measurements, patient records, images, etc.
Device/System | System Concerns | Communications Needs |
Analog Instrument | Needs a computer for conversion to digital format | Depends on the computer system and process. Normally TCP/IP file transfers (e.g., CSV files), may be interactive. |
Smart Devices | Serial, USB | Needs intermediate connection hub or computer |
Bluetooth, Wi-Fi | Network protocols, may need a PC for programming support. TCP/IP connections for LIMS access | |
IDS | File transfers | May need API to manage system interactions |
External (to the lab) | File transfers or database-to-database communications | TCP/IP file transfers. May need API to manage system interactions |
Table 1 – Summary of data/information interchange options
TCP/IP manages communications within laboratories and between labs and other organizations. There are two concerns, however. One is the nature of the communications (file transfers, or command/control sequences) and the physical connections needed. Table 1 (above) summarizes the major issues: getting lab data into a digital format and making the physical and programming connections (where needed). The most common use outside the lab for serial, USB, Bluetooth, and Wi-Fi connections is between devices through a computer with the necessary ports and the computer managing the interaction. How do we manage that in the laboratory? How do you do that when the LIMS is in the “cloud”?
LabVia product family is key to LIMS Integration
LabLynx has provided a set of products to make both of the aforementioned physical and programming connections. There are three components:
- LabVia Hub provides facilities for the serial, USB, and network connections needed to physically access the devices in your lab;
- LabVia Cloud provides the interaction between LabVia Hub, your lab’s computing systems, including instruments, to ELab LIMS;
- sciForge provides the application programming interface (API) for real-time and program-to-program interactions between ELab LIMS and other systems.
The result is the ability to connect your lab’s instrumentation to the LabLynx ELab LIMS whether the LIMS is on-premises or in the cloud. You have the tools you need regardless of whether your devices are connected through a computer or in the case of smart instruments, through the HUB/Cloud system to the LIMS. If programmed interactions are required sciForge will provide an API to assist you.
In closing…
Laboratories are unique in the variety of sources of data and information available to them. That variety can be perplexing when it comes to making connections between experiments, tests, and a LIMS you want to use to store and manage data, information, and results. That includes the bi-directional transfers needed to take advantage of automation capabilities that together with smart devices and instrument data systems help minimize or eliminate data entry errors, increasing confidence in your lab’s operations. The LabLynx LabVia family of products provides a pathway to realizing a solution to those needs.