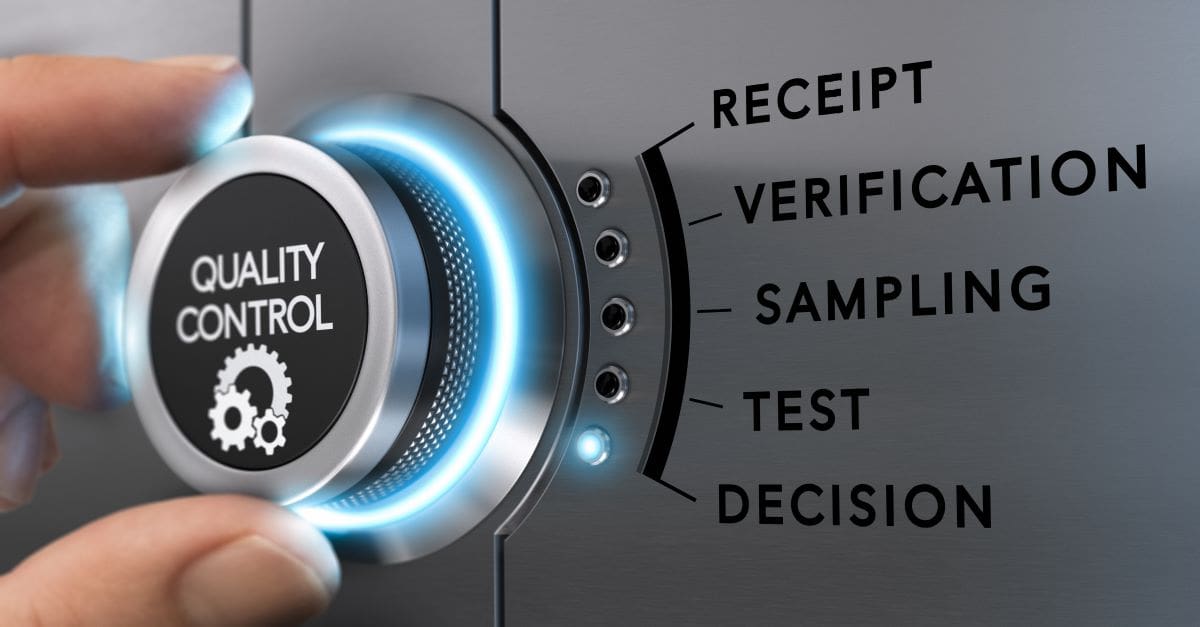
The history of laboratory informatics began in earnest with the commercialization of instrument data systems and LIMS software, the latter having the larger impact since it could affect the entire lab’s productivity and benefit the organization it supports. That software found a home in both industrial Research & Development, Manufacturing, and Healthcare (clinical laboratories). In each of these situations, LIMS provided a means of organizing and managing testing workflows and streamlining operations. This article is going to focus on the role LIMS software plays in the manufacturing segment of the market. It’s important because we are looking at a market segment that has developed software packages with some potentially overlapping capabilities (LIMS in the lab, and enterprise reporting/manufacturing execution packages in process control) and that can create issues in how software is selected and implemented.
Within a manufacturing facility, the laboratory has a limited and specific role: quality control (QC). Within that framework, it performs a specific set of tests to support incoming raw materials evaluation, process monitoring, and product testing/certification. Ideally, no raw materials are used in the manufacturing process unless they are certified for use by QC (although some organizations have special arrangements with vendors that make high-quality products), and nothing is shipped unless the QC process certifies it as suitable for shipment. While QC provides data/information to production, their lines of organizational reporting and responsibility are parallel and separate; the intent is to avoid conflicts of interest.
The organizational structure of a manufacturing company1 consists of three divisions:
- Finance: Managers of allocations, inventory control, accounting, and financial planning all report to the VP of finance.
- Operations: Production managers and the director of human resources report to the VP of
- Marketing: The sales manager, director of customer service, and distribution manager all report to the VP of marketing.
How does quality control, and by extension LIMS, interact with each of those groups?
Finance:
As we noted above, finance includes responsibilities for inventory control, both incoming raw materials and finished goods. Quality control certifies raw materials as suitable for use and products as ready to ship. If there are problems with either of those two points the finance and accounting groups make the determination of how to handle problems, relying on data/information stored in the LIMS to backup any course of action. As a result, they may request access to the LIMS software which is reasonable and can be granted with careful controls on privileges and what material they can view.
Operations:
This is the primary home of quality control and LIMS. The role of LIMS is to help facilitate lab operations and workflows, and, to serve as a repository for the data and information produced in the course of laboratory work. The workflow in the QC lab is different from that in other lab types that would use LIMS such as contract testing, or labs that support research. The production process imposes routine testing requirements that other labs don’t have. There may be a requirement for sample retesting but that is infrequent. QC doesn’t have the “walk-in service” that other labs have, its testing requirements are routinely the same day in and day out. The need for fast turnaround is always there, whereas other service labs may have more flexible requirements. We’ll get into this in more detail shortly.
Marketing:
QC and LIMS software have roles here as well. One aspect of the marketing department’s responsibilities is customer service. If a problem occurs with a product, a customer complaint for example, the data/information in the LIMS will be used as a first step in determining where the problem originated. Did everything meet specifications? Was there an issue with raw materials? Were other products made at the same time exhibiting issues?
The data contained in a LIMS has wide use in the manufacturing organization; we’ve only touched on a few points. This raises one concern however: where should that data/information reside? If a company is invested in enterprise resource planning (ERP) they will want the data/information to be in those data structures where it can be combined with material from other sources. Yet the lab would probably feel better about limiting access to the LIMS. One solution is to have the LIMS automatically send finished test results to the ERP software and have them parsed and stored.
Another is to integrate the LIMS as part of the ERP system.
That last sentence can raise a number of problems, starting with people not really understanding what a LIMS is, its functionality, and why it exists. When non-lab people look at a LIMS they see a database with features found in other software packages, including ERP systems. What they don’t appreciate is that a major component of the software is the ability to work directly with instruments, a feature that provides much of LIMS productivity benefits. Another is the availability of a user community to push the development of the product to new levels of utility, something a build-your- own system will lack. For a more detailed discussion on this topic see “LIMS Software: Build or Buy?”2
Types of manufacturing
There are three types of manufacturing that we are going to focus on: continuous, batch, and discrete operations. In each of those types of operations, QC has responsibilities from one end of the production cycle to the other. In the third type of production, discrete manufacturing (e.g., cars, cameras, phones, toys, etc.) the role of the testing lab, and hence LIMS is often limited to incoming raw materials testing and component evaluation.
Continuous (process) manufacturing
The production of pasta, juice, ice cream, and petroleum distillates are all examples of continuous manufacturing. In most cases, the production of the product proceeds without disruption until the end of the process when the product is packaged for distribution and sales. There are exceptions to that; the writer once worked in a lab that was part of a partnership between a natural gas refining company and plastics raw materials producer. The refinery continuously produced monomers (ethylene and propylene) which passed through a pipe under a road to the plastics producer where it continuously polymerized to polyethylene and polypropylene homopolymers and copolymers. At the end of the process the plastic pellets were packaged into 1000 lb. boxes (the continuous production converted to a batch operation).
LIMS supports these types of production operations by providing a means of scheduling and organizing testing of samples taken at strategic points along the process as well as the final product to ensure that there weren’t any deviations from expected operations and that the resulting product met the criteria for salable goods. The information produced in a QC lab goes to shipping to certify that product is ready to ship, and to process control to let them know that the sampling points along the process are within expected tolerances for the product being made. In addition, the lab monitors incoming raw materials to ensure that they are suitable for use in product production. The testing protocol for products is pretty similar since the production line is designed to produce specific items. The QC information contained in the LIMS is part of the data/information stream that production used to determine whether products are consistent with specifications and processes are running normally.
LIMS originally grew from labs using manual methods of analysis, then embraced instrumentation within the lab as well as automation. What about automated instrumentation outside the lab? Online or inline testing at key points within the production process is common. The purpose of this instrumentation is to provide more frequent measurements of key process parameters with the results being passed to process control. Who has control over these devices is going to be dealt with differently by different companies. Ideally, the responsibility for device maintenance, calibration, and test results should lie with QC to ensure data and system integrity, avoiding conflicts of interest should measurements drift from production requirements. There is the potential for the role of the QC lab to become reduced to an equipment service group as more automation is used and efforts are made to bypass QC, with test results going directly to process control. As such, some of those doing QC work may find their role changing to ones that ensure the automated equipment is operating properly, with periodic checks on calibration and performance. How this plays out is going to vary widely depending on the nature of the process, cost, and the type of product being produced.
Batch manufacturing
Baked goods, computer chips, and flat-packed furniture, are all examples of products produced by batch processes. Take pizza for example. The process can take different directions depending on the quantity being produced and variations in the recipe; every pizza having different toppings vs. making a lot of the same kind of pizza in commercial production. In the former case, one person may execute the entire recipe from preparing the dough to putting it in the oven and monitoring the cooking process. In mass production3, a series of stations would be set up to carry out a series of individual steps in the recipe until it is time for packaging and freezing. Along the way, inspections are carried out to ensure product quality. The role of the QC lab is to evaluate the product in different stages, as well as the incoming raw materials, and ensure the raw materials (RM), the developing product at intermediate product (IP) stages, and the final product (FP) all meet the expected standards for quality. For each product produced there are master production records (MPR) providing the idealized product recipe and batch production records (BPR), listing what materials were used and the associated test results showing how close each batch approaches the ideal model. The information for the BPR is derived in part from the LIMS. For example, the MPR would say to use a certain amount of material in a particular step. The BPR would take data from the LIMS to say that the product was tested, and what quantity of material was used, and from what vendor batch it was made (along with its certification results), was actually found in the product.
Specification and test group management defines the required testing for the product and RM test management. These, plus any expected value ranges can be built into a LIMS as part of the group testing and result’s management of a LIMS. That plus the MPR and BPR, could take advantage of the LIMS document management facilities to both ensure document access control and security. As master production records are updated, the LIMS test groups can be updated all within the same system. This can be done in other manufacturing software as well.
Discrete manufacturing
Batch production makes large quantities of products that might be packaged as individual units (e.g., cosmetics) or in quantities in packages (e.g., a pound of cookies in a box). Discrete manufacturing is similar, but the quantity of products produced is smaller.
The writer’s experience with LIMS is within the framework of lab bench science; and considering an airplane or refrigerator as a sample would be a stretch. However, LIMS does have a role in this type of manufacturing. LIMS is designed around a behavior model (see list of articles at the end of this piece), not a type of testing. This stands in contrast to the laboratory information systems (LIS) in the clinical lab, which has similar attributes to QC, but are designed around both a workflow model and types of testing. Incoming raw materials testing, including chemical and component tests (e.g., evaluating the optical components in a camera, testing small motors) are tests we can see taking place on a lab bench. In other words, it’s not the type of testing that matters, it’s how the results are managed. The concepts behind BPR can be applied here, as well as in batch manufacturing.
Manufacturing software
There are several software packages that are used in manufacturing environments:
- ERP (noted earlier) is used to manage day-to-day business operations in a company (e.g., accounting, procurement, project management, etc.)
- Manufacturing execution systems (MES) are used to track and document the transformation of raw material to finished goods, and,
- Product lifecycle management (PLM) is used to manage product conception and design, development, production and launch, service and support, and retirement. The LIMS has historical product quality information that can support reviews of evolutionary operations programs4, and general product quality reviews, as well as track product quality issues and support their cause and resolution.
Each of these has some overlap with LIMS software functionality (more with ERP and MES, less so with PLM) and as a result, people will try to “simplify” their software by taking something they are familiar with and making it look like a LIMS. This approach is not recommended. These are distinctly different packages with specific functionality needed to accomplish their purpose. They shouldn’t be modified to make them look like something they aren’t. What does make sense is to allow a LIMS to communicate with ERP, MES, PLC to exchange data/information. Message transfers are preferred to “integration” since integration may involve programming changes that may not survive upgrades or violate warranties5, or otherwise compromise software integrity.
LIMS software supports manufacturing beyond the normal sample tracking model with:
- Automated sample login / acceptance / tracking / report
- Control charts for sample results and reference
- Incoming raw material
- Production of “ready to ship” certification with communication to production, and shipping/receiving.
- The use of internal standards to support data integrity and system
- The ability to support regulatory
- Support for non-routine sample
- Equipment calibration and maintenance support for both in-lab instruments and in-line
- Reagent materials
Future directions in LIMS software for manufacturing
Software development for laboratories, manufacturing facilities, and other industries has been going on for over half a century. The approach has always been the same: we are focusing on this problem in this market often with blinders on when it comes to coordination with other software systems in the same or functionally related groups/departments. Coordination between systems is left as an exercise for the user. We need an objective standardized methodology for allowing two or more systems to interact with each other. It’s been done successfully in the clinical lab market, and with computer graphics, communications, social media, and others. The result is always the same: better systems, better support, and an explosion of applications that benefit the user community and vendors. Rather than trying to reproduce full LIMS functionality in an ERP system, instead provide a standardized link to exchange data and information to help ensure they are where they need to be to gain the most value from them.
References
1 https://bizfluent.com/facts-6942091-organizational-structure-manufacturing-company.html
2 https://www.lablynx.com/library/articles/lims-software-build-or-buy/
3 To view the process of mass-produced pizza see: https://youtu.be/E3MmpvHl7MM
4 Evolutionary operations programs (EVOP) are efforts to optimize production through a series of small process changes
5 For a related discussion see: “QC Manufacturing Data Coordination”: https://www.linkedin.com/pulse/qc- manufacturing-data-coordination-gloria-slomczynski/
This is the sixth entry in this series, the previous articles have looked at:
- What Laboratory Information Management Systems (LIMS), Scientific Data Management Systems (SDMS), Laboratory Execution Systems/Functions (LES), and Electronic Lab Notebooks (ELN) are, (https://www.lablynx.com/news-events/what-is-a-lims-eln/)
- Compared two different methods of implementing a LIMS (on-premise vs the cloud) (https://lablynx.com/news-events/choosing-a-lims-technology-cloud-based-or-on-premises/),
- Reviewed how a LIMS works and can improve your lab’s operations (https://www.lablynx.com/news-events/how-does-a-lims-work/),
- What is the Ideal LIMS for Your Lab? (https://www.lablynx.com/news-events/what-is-the- ideal-lims-for-your-lab/) and
- LIMS Software: Build or Buy? (https://www.lablynx.com/library/articles/lims-software-build- or-buy/)