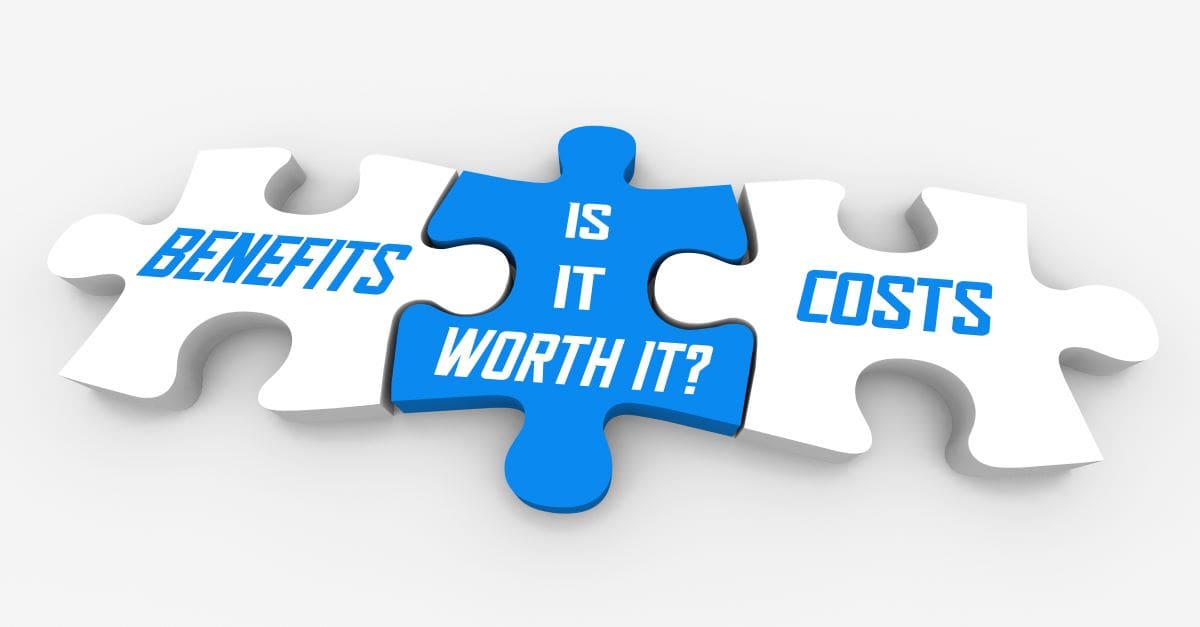
Laboratory work depends upon highly skilled people and sophisticated equipment to produce knowledge, information, and data. The cost, value, and ROI for those products are affected by the methods used to record and manage them. Paper-based systems are high-cost (once you account for the labor in their use) and have a lower return on your investment, while electronic systems provide increased efficiency, easier access, and greater utilization with a higher ROI. Producing knowledge, information, and data is one key aspect of laboratory work. Keeping it useable, accessible, and searchable over the long term is key to maintaining its value and realizing the return on your investment in laboratory space, equipment, and personnel.
This article will look at the return on investment or ROI in laboratory informatics and provide you with information you can use to evaluate expenditures on software, hardware, and methods of implementation. The topics covered include:
- Introduction to ROI
- Comparison of operational models: paper-based vs. informatics
- Informatics beyond laboratory information management systems (LIMS) and electronic laboratory notebooks (ELN)
- Factors affecting ROI realization
- Expectations of productivity and ROI: are they realistic?
Introduction
Evaluating ROI is a matter of comparing the difference between two operational models: the one you have now and one with informatics added. The “return” on the investment in informatics is the difference in operational performance, some of which can be realized in dollars, improved efficiency, cost avoidance, and other factors. Your investment is going to be continuous in either model, so it really comes down to two questions:
- How does the level of investment vary between the two models?
- Is that investment yielding the operational performance you need?
Model 1: Paper-based record keeping
Paper-based models of record keeping (e.g., paper notebooks, charts, tables, etc.) are a convenient place to begin since they are common in startup labs beginning their operations, and most of us have dealt with those tools in undergraduate work. Most paper lab notebooks are bound, have a table of contents, and have paired pages structured so that writing on one page leaves an impression on the next page automatically creating a backup copy. There is room at the bottom of the pages for signatures and dates for the author of the work and a witness (required by most labs and regulatory groups).
The investment in paper-based systems is initially in two parts: the acquisition of the notebooks themselves, and the creation of the content. Notebooks are low cost, which makes them initially attractive. The content may reflect many thousands or tens of thousands of dollars in work utilizing expensive equipment and materials. The return depends on your ability to gain value from that investment.
Since the notebook is paper, with handwritten notes, pasted in printouts, charts, graphs, etc. working with a notebook’s contents is expensive. It depends on people putting in effort (more expense) to organize and work on the results of experiments. There are two additional problems with paper notebooks beyond the cost of working with the contents committed to them: their ability to be damaged and the loss of working access to data/information written into them.
Paper notebooks can suffer all the ills that anything written on paper can be subjected to including spills, torn pages, loss, etc., all of which can affect the ability to work with lab-produced data. Unless you make copies of each day’s work, there is no backup for recovery. Beyond that, there is the possible loss of access to the contents of the notebook in its entirety.
Once a notebook is filled, the author may keep the second of the paired pages (the equivalent of a carbon copy) for their records and the book itself is likely placed in the lab’s or organization’s library for short-term storage. Moving it to long-term storage – the archives – can occur after a period of time, and, as a consequence, the material becomes difficult to search assuming anyone remembers it exists. This highlights a common problem in the paper-based lab: the loss of institutional memory as people change jobs either within an organization or leave altogether. Once that happens, the material is often forgotten and the return on investment goes to zero. Depending on the nature of the archives that can also happen as a result of damage to notebooks from water or rodents. Your investment in a project is only valuable as long as it is accessible.
There are ongoing costs with paper-based systems in the form of people’s efforts and time. Let’s examine paper-based service labs – those that do testing such as analytical services and physical testing.
- In the paper-based lab, samples and test request forms are submitted and logged in with a sample ID assigned. That sample ID is entered on the test request forms and the sample itself. The sample is stored and the location is noted. In a medium to large lab, this and the associated administrative work can require the equivalent of a full person’s time.
- If an analyst is checking to see what work has to be done – they may be running a particular test and want to see if other samples need to be processed – they would examine the log book and test request forms to create a worklist.
- The analyst would then have to gather the samples and begin processing.
- If a submitted sample has multiple tests they may have to check with other analysts who may have that form.
- When the work is done and approved, the analyst would have to enter the results on the sample request form and log the request as completed if no other testing is being done.
This is a completely manual process that builds inefficiency in lab operations, increasing daily operating costs.
Paper-based systems also make it difficult to meet regulatory requirements. The possibility of data loss is one point. Another is pointed out in a recent (2022) American Pharmaceutical Review article[2] which asks: “Why are the top 10 FDA Form 483 issues mostly the same for the past twenty-two plus years? What is the cause(s)?” Among the answers, one finds that: “many small firms are still paper-based, and do not have the necessary money and technology to analyze process and analytical data in such a way that allows for proactive responses to trends.” While the article is specific to FDA requirements, the same set of issues can likely be found in labs across the industrial spectrum. Note: the process analysis referenced in the article is a normal part of implementing informatics systems.
While paper-based lab operations may appear to run well, their limitations are going to be felt as the lab and workload grow. This applies to both service and research groups.
Model 2: Laboratory informatics
The equipment and investment of effort in laboratory informatics are higher than in paper-based procedures, but the payoff is considerably greater. That investment consists of:
- Peoples time in getting educated so that they can make informed decisions about products;
- The cost of implementing systems which can vary widely depending on whether you choose the on-premise model or cloud hosting (no hardware or IT services needed); and
- On-going periodic license payments for access to the software.
The return on that investment will take several forms. Let’s start by comparing the prior-mentioned paper-based service lab operation above with the equivalent LIMS-based informatics method.
Table 1 – Comparison of Paper-based systems and LIMS
One of the significant returns on investment in informatics is a reduction in human labor which can help avoid the need to increase headcount. Table 1, above, is a first pass at the benefits. All of the LIMS activities noted in Table 1 can be carried out concurrently by multiple users, unlike paper-based operations. With a well-integrated informatics system – e.g., a LIMS connected to lab instruments with an autosampler for automatically introducing the sample into the device, -the worklist of samples to be processed can be sent to the computer supporting the instrument, the samples processed, and the results electronically entered back into the LIMS when the work is completed. This represents a considerable increase in efficiency and allows for 24/7 operations.
One of the problems noted earlier in paper-based systems was the potential for loss of data/information for several reasons. With informatics, once the data is entered, it is readily available regardless of when it is recorded. A simple electronic search will find it.
Putting the results of the work in an environment (i.e., a LIMS) that fosters a high rate of utilization and availability (i.e., knowledge and intellectual property management) happens through the development and implementation of a well-structured informatics architecture. That architecture will provide a basis for future growth and innovation. It will also encourage the consolidation of data/information instead of having it spread over multiple systems. Documents like monthly reports of analysis can be generated automatically. Data can be searched, extracted, and used with statistical analysis programs easily, or forwarded to a researcher who needs access to it.
How does this contribute to your lab achieving its ROI and performance goals?
Service labs
- Reduced administrative overhead
- Better/more productive use of lab personnel’s time
- Faster analysis turn-around and higher productivity
- More effective use of resources
- Ability to quickly search all electronic records and access all electronic laboratory data/information
- Improved ability to meet regulatory requirements
- Long-term reduced cost of operations
- Streamlined operations
Research labs
- Better record-keeping and access to all electronic lab data/information
- Improved ability to work with and gain value from all research data/information lab-wide, and across the organization
- Lower administrative costs
- Improved ability to execute experiments and move projects forward
- More effective use of lab personnel, reducing the need to increase headcount
- Lower program/project costs
Informatics beyond LIMS and ELN
There are additional informatics elements beyond LIMS and ELNs that can help improve productivity, improve the ability to meet regulatory requirements, and further streamline lab operations:
- Scientific data management systems (SDMS); The SDMS provides a means of organizing data files from instruments, images, documents, etc., that can’t be stored in a LIMS or ELN.
- Laboratory execution systems (LES); The LES is designed to provide a rigorously faithful execution of a lab procedure by an analyst, capturing data as it is produced and ensuring that equipment and reagents are suitable for use in the method (e.g., ensuring equipment is properly calibrated and maintained, reagents are not out of date, etc.). An LES can be connected to both a LIMS and ELN for data transfer.
- Instrument data systems (IDS); The IDS controls one or more lab instruments (of the same type), can receive worklists from a LIMS, and report results back while automatically storing them with the sample’s information.
LIMS and ELNs are not the only elements that go into improving productivity in lab work, however; they are simply the top tier of administrative and workflow management systems. There are a variety of forms of automation that contribute to the overall improvements in lab operations. They include autosamplers, computer-controlled instruments, and robotics for sample preparation, as well as others that allow for the creation of an assembly-line-like environment. Some techniques lend themselves to this level of automation more than others, and people need to be trained to take advantage of the potential for automation in their work.
Factors affecting ROI realization
Before we go further, there are some issues that need to be addressed in the pursuit of gaining the highest ROI. Considerations include planning, education, support, custom-built solutions, and spreadsheet pitfalls.
Planning
Many labs grow “organically”, adding systems as needed. These systems have the ability to improve productivity and your ROI if they are used properly. There are labs that have instruments connected to data systems (i.e., the IDS) that print out pages of results that are then walked over to a LIMS and manually entered into that system (requiring a second person to verify the data entry). Why not connect the two systems and allow the data to be entered automatically? Planning ahead is essential. What systems do you need? How will they be used? Can they be connected to the LIMS or ELN? These are just entry-level questions.
Education
Unfortunately, laboratory informatics is almost never taught in schools. Education is informal, at the most encompassing short courses. Laboratorians need to understand what these systems are, how they work, and how to plan for and apply them.
IT and vendor support
You’ll want to work with IT people and vendors who understand what you are doing and what is needed for your lab to be successful. IT requirements that might work in an office may not work in a lab due to the diversity of systems and vendors (see Table 2 for a comparison of office and lab IT support environments). Good vendor relations are essential. The following table compares office and lab IT support environments:
Table 2 Comparison of corporate and lab IT support environment[3]
Custom-built software
Avoiding the idea of building your own software unless it is absolutely needed. Then really think about it again. Essentially you are creating a software development project that will continue for the life of the product’s use, continually adding costs. That is what software vendors do. See “LIMS Software: Build or Buy?”[4] for more details on this subject.
Spreadsheet pitfalls
Avoid using a spreadsheet to fulfill the need for a LIMS. Spreadsheet software has some very good uses, but emulating a LIMS isn’t one of them. The size of the spreadsheet will grow quickly and become unwieldy to work with. If nothing else, you will find yourself scrolling vertically and horizontally trying to find information on samples, and never have a complete view of a sample’s data and information. There is always the potential for data loss without any recovery. When you do upgrade to a LIMS, there is the issue of incorporating the spreadsheet data into the new software or living with the “old system” vs. the “new system”. In addition, there is always the ongoing cost of maintaining the spreadsheet database, adding features, etc. without losing the integrity of the original system.
The top-tier informatics systems – LIMS and ELN – are the core of a laboratory’s digital strategy. They are, ideally, the places where data and information generated in the lab are stored. They are the foundation that new knowledge is built.
Is higher productivity and ROI a realistic expectation?
The answer to this question basically depends on having the people you need and thinking through the need for automation and its realistic application (for more on this see Considerations in the Automation of Laboratory Procedures[5]). As to how realistic it is, work in the clinical chemistry industry has demonstrated what planning for end-to-end automation can achieve.
In the 1980s the clinical chemistry industry had a problem: they quoted their customer’s annual fixed-price-per-test contracts and during those years the cost per test continued to rise without the availability to recover those increasing costs. They worked on the problem as an industry and arrived at a solution: Total Lab Automation. That meant end-to-end automation that included laboratory informatics systems. They did, however, have one advantage that other industries should consider: their testing procedures were standardized across the industry. This meant using the same procedure and the same or similar equipment that was designed for use in an automated environment and pre-validated for that purpose. The TLA model was put to use across the industry. The results of one study published in 2003[6] demonstrate TLA’s’ effectiveness (note: that robotics was an important component of this work):
“Results: Between 1965 and 2000, the Consumer Price Index increased by a factor of 5.5 in the United States. During the same 36 years, at our institution’s Chemistry Department the productivity (indicated as the number of reported test results/employee/year) increased from 10,600 to 104,558 (9.3-fold). When expressed in constant 1965 dollars, the total cost per test decreased from 0.79 dollars to 0.15 dollars. Turnaround time for availability of results on patient units decreased to the extent that Stat specimens requiring a turnaround time of <1 hour do not need to be separately prepared or prioritized on the system.
Conclusions: Our experience shows that the introduction of a robotics system for perianalytical automation has brought a large improvement in productivity together with decreased operational costs. It enabled us to significantly increase our workload together with a reduction of personnel.”
The results noted above are heavily influenced by the replacement of manual labor with robotics and information systems. The work also includes the development of data interchange standards between an IDS and an LIS (laboratory information system, i.e., the clinical lab version of LIMS). Similar results are found in other publications including “Improving Laboratory Processes with Total Laboratory Automation[7]” and “Advantages and limitations of total laboratory automation: a personal overview.[8]”
When dealing with automation, the return on investment requires a long-term view due to the need for planning, product selection, implementation, and giving those working in the lab time to come up to speed on their education and the use of the systems that are being put in place. A well-thought-out digital lab architecture and strategy is the foundation for your lab’s success.
Footnotes
[1] “Selecting Products for Lab Automation”, John Trigg, phase Four Informatics Ltd, European Lab Automation 2013 Conference, Hamburg, Germany[2] Lynn, S.J., “A Discourse on Pharmaceutical cGMP FDA Form 483 Trends: Why are We Re-Living the Same Issues Over the Last 23 Years?”, American Pharmaceutical Review, Volume 24 Issue 4, May/June 2022, pgs 72-78
[3] Liscouski, J., “Computerized Systems in the Modern Laboratory: A Practical Guide”, PDA, Bethesda MD, 2015, https://www.pda.org/bookstore/product-detail/2684-computerized-systems-in-modern-lab
[4] https://www.lablynx.com/library/articles/lims-software-build-or-buy/
[5] https://www.limsforum.com/ebook/limsjournal-laboratory-technology-special-edition/ [6] Clin Chim Acta. 2003 Mar;329(1-2):89-94. doi: 10.1016/s0009-8981(03)00020-2[7] Laboratory Medicine, Volume 50, Issue 1, February 2019, Pages 96–102, https://doi.org/10.1093/labmed/lmy031
[8]From the journal Clinical Chemistry and Laboratory Medicine (CCLM) https://doi.org/10.1515/cclm-2018-1323