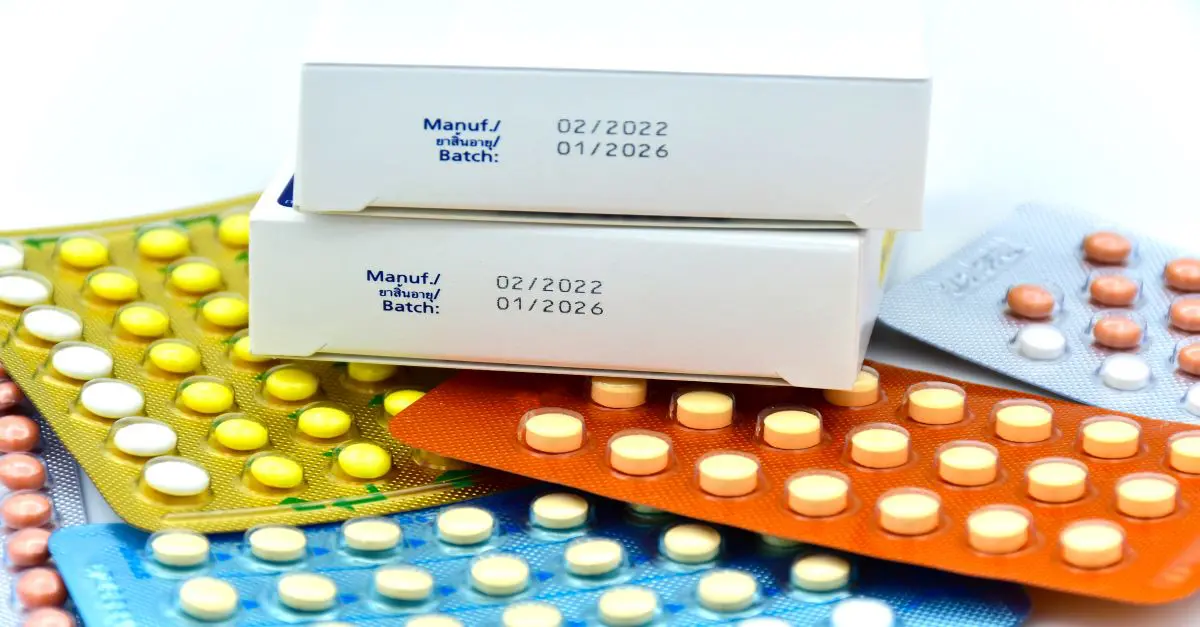
One question that might have crossed your mind as a consumer as you reach in the fridge towards that questionable half gallon of milk to accompany your freshly poured cereal bowl is, “do these dates really matter?” The same can be said for over-the-counter medications, pharmaceuticals, and numerous other consumer items.
One common misinterpretation is determining if expiration dates refer to food quality or safety. Expiration dates are in place to determine optimal food quality for consumption. These dates are not a sign of a product’s safety, except for infant formula, and they are not required by federal law. [1]
To assist customers and retailers in determining when food, pharmaceuticals, and other products are at their best, manufacturers supply expiration dates. Expiration dates are calculated using stability studies that determine the shelf life of materials or products. They often take into account the conditions under which it is stored and the average degradation rate.
Expiration dates and shelf life
Accurate expiration dates on consumer packaging are crucial to keeping the public safe because they deter shoppers from potentially consuming products past their prime, avoiding illnesses from unsafe products.
These dates are determined by invaluable research using consumer shelf life studies, which are inherently based on stability studies. The primary focus of these studies is to alert users when a product or material is approaching the end of its shelf life.
Real-time stability tests are used by manufacturers to determine a product’s shelf life. The shelf life of a food product is “the period of time that a food product is considered acceptable for consumption when stored at the appropriate storage conditions,” according to the Institute of Food Technologists (IFT) and the National Advisory Committee on Microbiological Criteria for Foods (NACMCF). [2] In the United States, almost all foods, medicines, and other consumable products must have a clearly marked expiration date.
Studies on shelf life are used to establish how long a product or material may be kept in storage without compromising its safety or usefulness. These investigations are usually carried out to ensure that a material or product is of good quality and safe to use for a certain amount of time.
Stability studies are also regarded as a requirement for the acceptance and approval of any pharmaceutical product since they guarantee the maintenance of product quality, safety, and efficacy during the shelf life. These studies must be carried out methodically, per the standards set by the ICH, WHO, and other organizations. [3]
With the importance of these stability studies across multiple industries, it is imperative the labs conducting them seek a laboratory informatics solution that allows them to operate as efficiently and as accurately as possible.
Stability studies
Stability testing intends to show how a drug substance’s or drug product’s quality changes over time under the effect of various environmental conditions, such as temperature, humidity, and light. Stability studies are vital in health and safety operations, including for the expiration dating and human drug product testing conducted by the U.S. Food and Drug Administration (FDA). [4]
Sample management that begins from the very beginning of the sample lifecycle is essential due to the volume of samples that must be handled, the length of time over which they must be monitored, the possibility of numerous storage sites and handlers, and other potential variables at play.
Stability testing management
Stability testing must consider sample and storage management, which frequently involves managing many levels of storage, including rooms, racks, shelves, and so forth. Informatics systems like the laboratory information management system (LIMS) aid in automating this monitoring and documenting, ensuring the accuracy of the data gathered. Careful documentation of storage conditions and history is essential to assuring accurate stability testing results.
To ensure an efficient and effective laboratory operation in those that conduct shelf-life stability studies, specific attributes must be in place within the laboratory environment to ensure a smooth research flow. Various analytical methods using high-performance liquid chromatography (HPLC), liquid chromatography–mass spectrometry (L.C.–M.S.), and gas chromatography (G.C.) are often used to test for the degradation of products. Separate testing is used to determine the sterility of products and whether the packaging of the final product is compromised.
This research process is multi-faceted and often includes the following:
- Tracking the transportation and storage of goods, including the people who handled them, the circumstances surrounding their handling, and the locations in which they were kept or transported.
- Estimating a product’s or material’s shelf life based on details such as the product’s use-by date, the storage environment, and the rate of deterioration over time.
- Providing users with an alert when a product or material is about to reach or has reached the end of its shelf life.
- Producing reports on the shelf life of goods or materials that include details on their expiration date, storage requirements, and any pertinent warnings or notifications.
- Stability test scheduling and management, including the capacity to designate tests for particular users, establish test frequency, and monitor test progress.
Managing stability studies can rapidly become challenging within a laboratory environment. Samples must be prepared for testing according to the study’s methodology and stored for years in particular environmental conditions. Since entities like the ICH and FDA have guidelines that do not outline testing methodologies, it may be necessary to validate new or updated methods.
Laboratory information efficiency
In order to prevent problems brought on by personnel turnover, long-term research must have clearly established protocols and workflows that remain consistent over time. Because of this, stability testing laboratories need an informatics solution tailored to their particular requirements.
Such information management solutions ensure that the findings of research operations and the fruits of the labor of laboratories are efficiently tracked and monitored.
LIMS or other informatics tools can positively impact a research facility’s operation by allowing for streamlined sample processing, reporting, sample tracking, inventory management, and more. Effective laboratory information management practices can also improve the quality and consistency of testing outcomes.
Not all laboratories serve the same purpose, which requires a flexible and configurable LIMS to be available for laboratories with specific needs. A well-designed, configurable LIMS aids in determining tracking parameters in a research environment. LabLynx provides such a LIMS, ELab, allowing users of all industries and backgrounds to enjoy a laboratory informatics experience that works best for their operations.
References
[1] USDA (n.d.). Food Safety and Inspection Service. https://www.fsis.usda.gov/food-safety/safe-food-handling-and-preparation/food-safety-basics/food-product-dating. [2] Righi, C. (2022, February 16). Predicting Product Shelf Life Through Accelerated Studies. Mérieux NutriSciences. https://www.merieuxnutrisciences.com/na/predicting-product-shelf-life-studies-through-accelerated-studies/. [3] Office of Regulatory Affairs. (2014, November 7). Expiration Dating and Stability Testing for Human Drug Products. U.S. Food And Drug Administration. https://www.fda.gov/inspections-compliance-enforcement-and-criminal-investigations/inspection-technical-guides/expiration-dating-and-stability-testing-human-drug-products. [4]Bajaj, Sanjay & Singla, Dishant & Sakhuja, N.. (2012). Stability Testing of Pharmaceutical Products. Journal of Applied Pharmaceutical Science. 2. 129-138. http://dx.doi.org/10.7324/JAPS.2012.2322.