Download Book For Free!
Resource Download
"*" indicates required fields
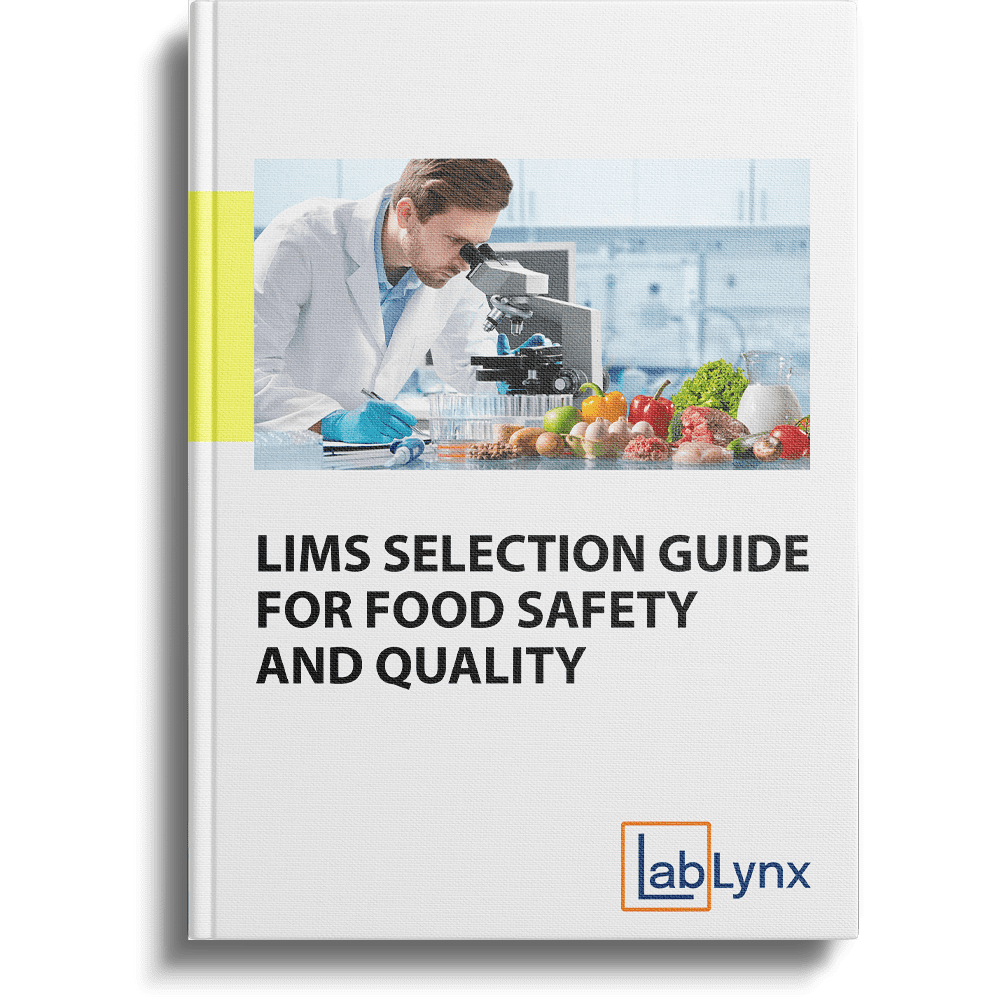
Choosing the Right LIMS for Food Safety & Quality Laboratories: A Comprehensive Guide
In the complex world of food safety and quality, laboratories play a crucial role in safeguarding public health. To meet stringent regulations, streamline operations, and ensure data integrity, a robust Laboratory Information Management System (LIMS) is non-negotiable. This guide will walk you through the critical factors to consider when selecting a LIMS specifically designed to meet the unique needs of food safety and quality labs.
The Importance of a LIMS for Food Safety & Quality Labs
A LIMS is more than just software – it’s the digital backbone of a modern food testing lab. A well-implemented LIMS can:
- Ensure Regulatory Compliance: Navigate complex regulations like FSMA, HACCP, and GFSI standards with ease.
- Enhance Traceability: Track samples from origin to final product, facilitating swift recalls if needed.
- Streamline Workflows: Automate routine tasks, reduce manual errors, and improve overall efficiency.
- Secure Data Integrity: Protect sensitive information with robust access controls and audit trails.
- Generate Actionable Insights: Analyze data to identify trends, optimize processes, and make informed decisions.
Key Features to Look for in a Food Safety & Quality LIMS
-
Regulatory Compliance:
- FSMA, HACCP, GFSI: Ensure the LIMS supports adherence to relevant food safety regulations and standards.
- Audit Trails: Maintain a comprehensive history of all actions taken on data for complete traceability.
- Data Integrity: Protect data against unauthorized access or modification with secure logins and role-based permissions.
- Document Control: Manage SOPs, test methods, and other critical documents with version control and approval workflows.
-
Functionality & Workflow:
- Sample Management: Streamline sample registration, tracking, and chain of custody.
- Test Management: Standardize testing procedures, manage calibration schedules, and track reagent usage.
- Environmental Monitoring: Monitor environmental conditions to detect potential contamination risks.
- Microbiology & Allergen Testing: Manage microbiological and allergen test results effectively.
- Reporting: Generate customizable reports for internal use and external stakeholders.
-
Integration Capabilities:
- Instruments: Seamlessly connect the LIMS with lab instruments for automatic data capture.
- ERP/MES Systems: Integrate with enterprise systems for efficient data exchange and process control.
-
Vendor Expertise:
- Industry Experience: Choose a vendor with a proven track record in serving food safety and quality labs.
- Customer Support: Ensure responsive and knowledgeable support throughout implementation and ongoing use.
- Training & Resources: Look for comprehensive training materials and ongoing educational resources.
Choosing the Right LIMS: A Step-by-Step Approach
- Needs Assessment: Define your lab’s specific requirements, pain points, and regulatory obligations.
- Research & Shortlist: Research LIMS vendors, compare features, request demos, and read customer reviews.
- Proof of Concept: Implement a pilot project to test the LIMS in your lab environment.
- Implementation & Training: Work with the vendor to ensure a smooth implementation process and comprehensive staff training.
LabLynx: Your Partner in Food Safety & Quality
LabLynx is a trusted provider of LIMS solutions designed to meet the unique challenges of food safety and quality labs. Our LIMS empowers you to:
- Maintain Compliance: Streamline your path to regulatory compliance and ongoing audits.
- Optimize Efficiency: Automate tasks, reduce manual errors, and free up valuable staff time.
- Elevate Data Integrity: Protect sensitive information with robust security features.
- Drive Continuous Improvement: Gain actionable insights from your data to enhance processes and make informed decisions.