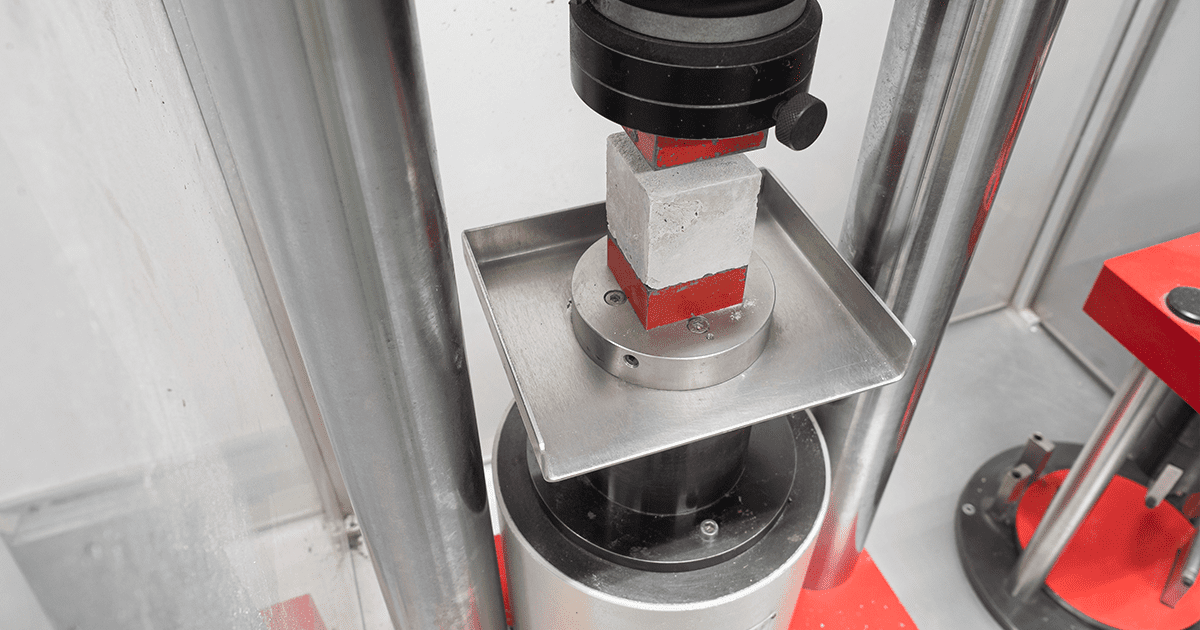
Materials testing laboratories play a critical role in ensuring the safety, durability, and performance of materials used across industries such as construction, aerospace, automotive, manufacturing, and consumer products. To maintain credibility and meet legal requirements, these labs must comply with a wide array of standards and regulations. Understanding these frameworks is essential for maintaining quality, achieving certification, and operating legally in today’s complex global environment.
Why Compliance Matters in Materials Testing
Regulatory compliance is not just about checking a box—it ensures the reliability of results, builds trust with clients, and protects public safety. Non-compliance can result in inaccurate results, liability risks, reputational damage, and the loss of certifications or contracts. Meeting industry standards demonstrates a commitment to quality, consistency, and scientific integrity.
Key Regulatory Bodies and Standards Organizations
Several national and international organizations develop standards that govern the work of materials testing labs. Some of the most influential include:
- ISO (International Organization for Standardization): Develops global standards such as ISO/IEC 17025 for testing and calibration labs.
- ASTM International: Provides thousands of standards, especially for mechanical, chemical, and environmental testing of materials.
- ANSI (American National Standards Institute): Oversees the development of U.S. voluntary consensus standards.
- NIST (National Institute of Standards and Technology): Provides guidelines for measurement science and laboratory practices.
- OSHA (Occupational Safety and Health Administration): Regulates workplace safety, including lab environments and chemical handling.
- EPA (Environmental Protection Agency): Enforces environmental compliance related to waste disposal and emissions from materials testing labs.
Top Standards That Impact Materials Testing Labs
Here are some of the most critical standards and regulations materials testing labs must be familiar with:
1. ISO/IEC 17025: General Requirements for the Competence of Testing and Calibration Laboratories
This international standard is the benchmark for quality and competence in testing labs. It covers technical requirements, personnel competence, equipment calibration, documentation, and quality control. ISO/IEC 17025 accreditation is often a prerequisite for contracts in regulated industries.
2. ASTM Standards
ASTM publishes more than 12,000 standards that define testing methods and procedures for virtually every material. Labs may follow ASTM E8 for tensile testing of metals, ASTM D638 for plastics, or ASTM C39 for concrete, among many others. Following ASTM standards ensures repeatability and compliance with industry expectations.
3. OSHA Laboratory Safety Standards
OSHA enforces regulations such as the Laboratory Standard (29 CFR 1910.1450), which requires a Chemical Hygiene Plan, proper training, and safety protocols. These are essential for protecting lab personnel and preventing accidents during material analysis involving chemicals or mechanical equipment.
4. Environmental Regulations (EPA)
Labs that produce hazardous waste or emissions during testing must comply with EPA regulations such as the Resource Conservation and Recovery Act (RCRA) and Clean Air Act. Proper waste disposal, chemical storage, and reporting are critical to avoid penalties and ensure environmental responsibility.
5. Good Laboratory Practice (GLP)
Originally developed by the FDA and now adopted globally, GLP outlines principles for planning, performing, monitoring, and recording non-clinical lab studies. While more common in biological or chemical testing, many principles apply to materials labs, especially when results impact public health or product safety.
6. Industry-Specific Regulations
Depending on the sector, additional standards may apply. For example:
- Aerospace: NADCAP accreditation and AS9100 standards.
- Construction: AASHTO standards for infrastructure materials testing.
- Automotive: IATF 16949 for automotive quality management systems.
Documentation and Record-Keeping Requirements
Accurate, complete, and secure documentation is required by nearly all regulatory standards. Materials testing labs must maintain detailed records of testing procedures, calibration logs, sample traceability, personnel qualifications, and quality assurance audits. Many labs rely on Laboratory Information Management Systems (LIMS) to automate and centralize these functions.
Accreditation and Auditing
To demonstrate compliance, many labs seek third-party accreditation from bodies such as A2LA, NVLAP, or ANAB. These audits assess conformance to standards like ISO/IEC 17025 and validate the lab’s technical competence. Preparing for these audits requires a rigorous internal quality management system and continuous improvement strategy.
How Lab Management Software Supports Compliance
Modern materials testing labs use lab management software to streamline compliance and stay audit-ready. Key features include:
- Automated workflows and standard operating procedures (SOPs)
- Digital traceability of samples and test results
- Real-time documentation and version control
- Integrated quality assurance and nonconformance tracking
- Secure access controls and electronic signatures
By integrating software solutions tailored to materials testing, labs can ensure regulatory compliance while reducing manual effort and minimizing human error.
Conclusion: Build a Culture of Compliance
Staying ahead of evolving regulations and standards is essential for the long-term success of any materials testing lab. Whether you’re testing concrete strength, plastic durability, or aerospace components, a deep understanding of industry requirements—and the right tools to manage them—can drive quality, trust, and growth. By aligning with globally recognized standards and investing in technology that supports compliance, your lab can lead the way in reliability and excellence.